A Global Leader within the Automotive Service Equipment industry struggled with disconnected systems and inefficient data management. We helped transform their operations, boosting efficiency and enabling smooth scalability.
SITUATION
A global leader within the automotive service equipment industry with 2000+ employees and revenues exceeding $800 million has been managing their organization with Excel spreadsheets and numerous custom applications with minimal interfaces. They decided to establish an ERP system to expand visibility on their financial health, centralize all company-wide transactions, enhance the customer’s expectations with accurate costs and lead times, and improve employee efficiency from top to bottom.
APPROACH
-
Collaborative Needs Assessment
UNCOMN was selected to collaborate with the leaders of each function to understand their needs and desires.
-
Process Mapping
UNCOMN's process mapping effort to map around 65 business processes provided guidance to our client.
-
ERP Selection
We assessed to implement an ERP to meet the client's wants and needs to improve efficiency from top to bottom.
-
Implementation Support
We supported the implementation through go-live and offer short term support to assist with issues that come up.
RESULTS
Strategic ERP Roadmap
Developed and facilitated business approval of strategic ERP assessment, selection, configuration and testing, and cutover roadmap.
Comprehensive Process Mapping
Created current, future, and a lesser amount of continuous improvement activity lists and 65 business processes across order to cash, manufacturing, finance, and new product development.
ERP System Matrix
Created large scale ERP system comparison matrix across all business processes above.
Enhanced Business and IT Alignment
Provided strategic and tactical business input to IT technology and functional business activities.
Joshua Hurst
Tech Lead
GROWTH & ENGAGEMENT
Reduction in Production Time
Improvement in Data Visibility
Cost Reduction in Operations
Related Case Studies
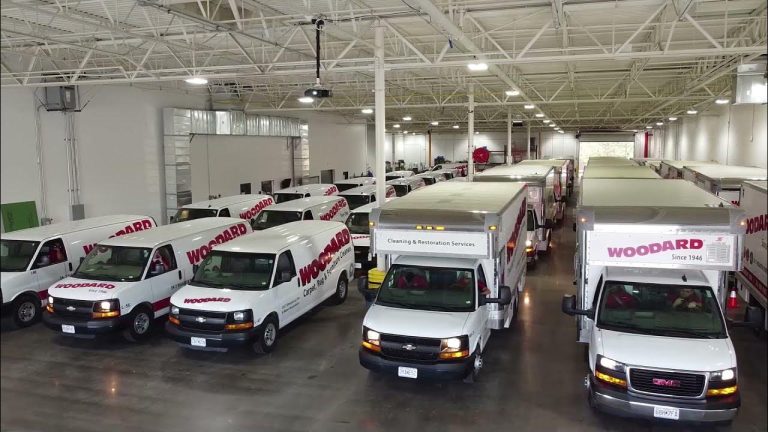
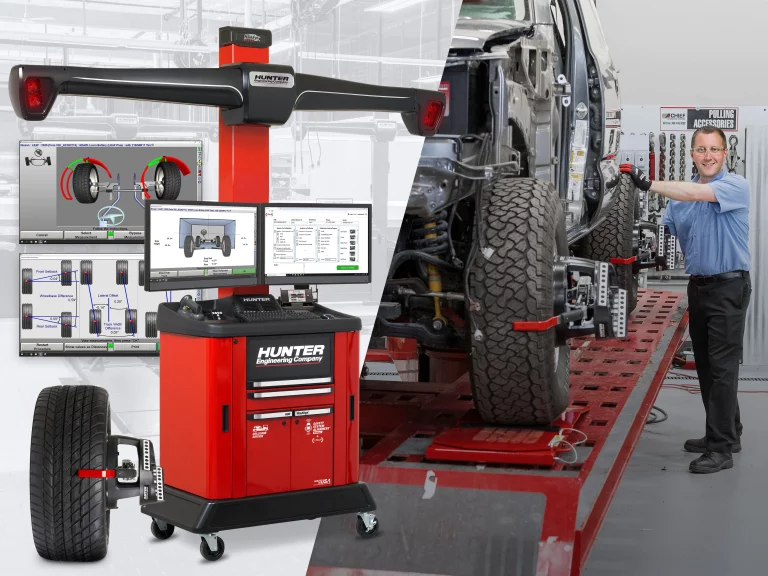
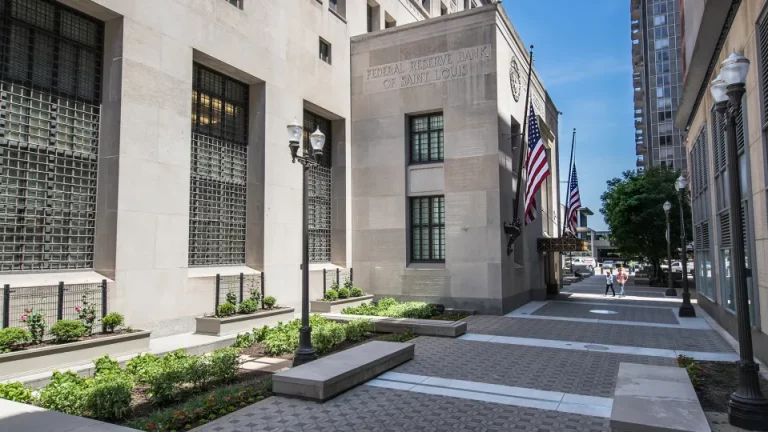
Federal Banking Institution
Securing the Cloud: Federal Banking Digital Transformation
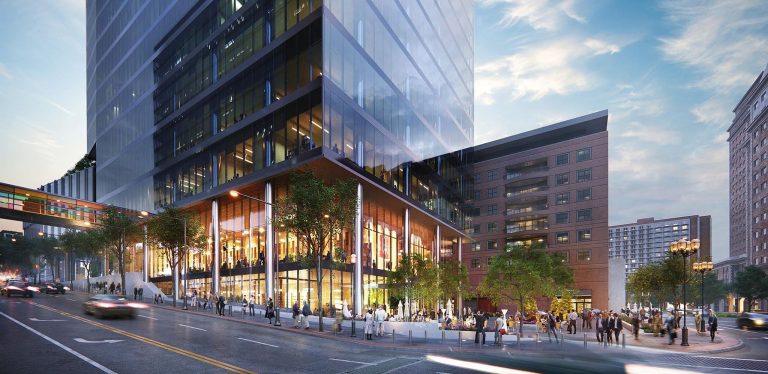
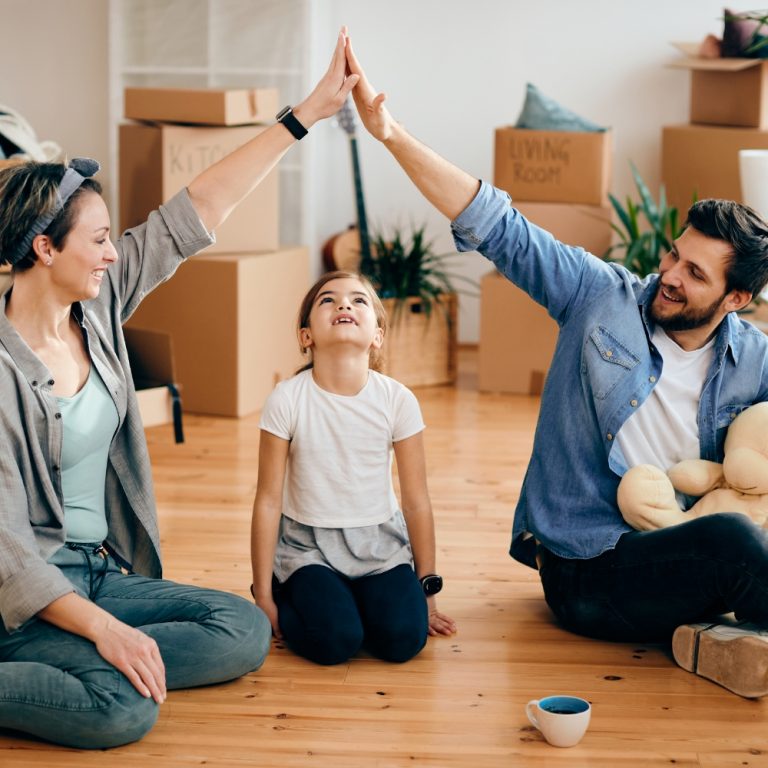
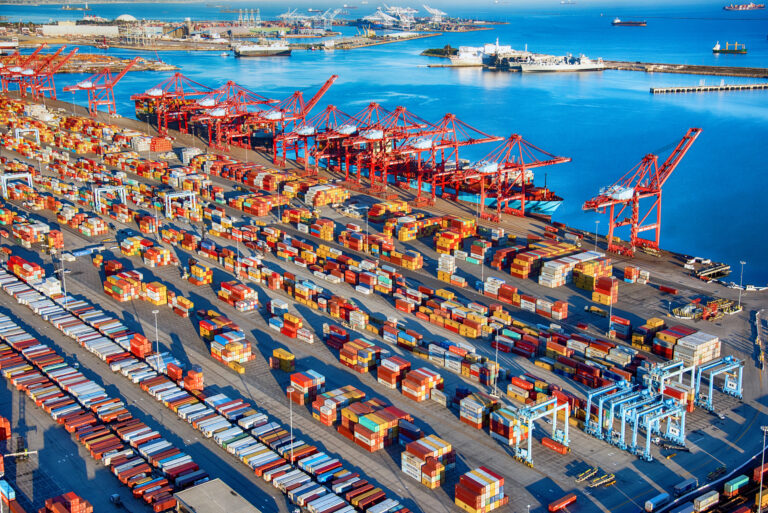